Employee Theft in Construction: How to Detect and Prevent Stolen Tools and Equipment
Employee theft isn’t always obvious—but it’s one of the most common ways construction companies lose money. Tools, gear, and materials can slowly disappear from your inventory without clear signs, and often, no one is held accountable.
In 2024, theft on construction sites in Europe resulted in losses exceeding €1 billion, according to Batinfo, with a large share attributed to internal incidents and lack of proper asset tracking.
Whether it’s happening in the field, in the warehouse, or during transport between sites, internal theft can quietly drain your profits. In this guide, we’ll walk through how to recognize the red flags, understand who might be responsible, and set up simple systems to protect your company’s assets before they go missing.
Why Tool Theft Is a Silent Profit Killer
Tool and equipment theft is one of the easiest ways money leaks out of a construction business—and often, owners don’t even notice until it’s too late.
It usually starts small. A missing drill. A few pairs of gloves. A laser level that was “left on another site.” But over time, those small losses add up fast. Suddenly, you’re replacing thousands of dollars in tools every year—and no one is being held accountable.
For small and medium-sized construction companies, these losses hit hard. You’re working on tight margins. Every piece of equipment you replace eats into your profits. And when tools go missing, it delays jobs, lowers productivity, and hurts your reputation with clients.
The worst part? Most employee theft happens gradually and from within—by employees, subcontractors, or people who have easy access to your job site. And without a system to track who used what, when, and where, it’s nearly impossible to catch.
That’s why tool and equipment management isn’t just “nice to have”—it’s a must. If you don’t track it, you’ll lose it. And if you don’t fix it, it’ll keep costing you month after month.
5 Red Flags That Point to Employee Theft
Employee theft doesn’t usually happen all at once. It’s often small, repeatable, and invisible—until you notice your budget’s bleeding and no one knows why. Here are five warning signs that aren’t always obvious but often point to theft happening under your nose.
1. You’re Replacing Basic Gear More Than You Should Be
If you’re constantly buying new gloves, safety glasses, batteries, or extension cords, that’s not just wear and tear. Consumables do get used up—but consistent overuse without an increase in jobs or headcount is suspicious. These smaller items are easy to pocket and resell, and they’re often the first to disappear.
2. Tools Only Go Missing from Certain Sites or Crews
Pay close attention to patterns. If missing tools keep getting reported from the same job site, or under the same foreman or crew, something’s not right. Maybe there’s poor oversight. Maybe someone’s taking advantage. Either way, tools don’t just vanish randomly—it’s usually systematic.
3. The Same Tools Keep “Breaking” or Getting “Lost”
Some tools seem to disappear more than others—especially items that are easy to resell or reuse off the clock (like power tools, batteries, or laser levels). If a certain category of equipment is always being written off as broken, misplaced, or transferred to another site without documentation, dig deeper. It’s often a cover story.
4. Inventory Numbers Don’t Match Actual Stock
If your inventory list shows 10 drills but you can only find 7, there’s a problem. Discrepancies between what’s logged and what’s physically available are one of the clearest indicators of asset mismanagement—or theft. Even if you’re not running full audits, spot-checking a few items weekly can uncover patterns.
5. Employees Push Back on New Tracking Systems
When you introduce better tracking, and someone immediately complains that it’s “too much” or “slowing things down,” ask why. Honest crews welcome structure—it protects them from blame. Resistance can be a defense mechanism from people who’ve gotten used to zero accountability.
Who’s Taking Your Gear? It Might Not Be Who You Think
When tools or equipment go missing, the first instinct is often to suspect employee theft. But the truth is, theft on construction sites doesn’t always come from the people you expect. In fact, assuming it’s just “employee theft” can cause you to overlook the real risks.
Here are the most common types of theft—and the people behind them:
1. Opportunistic Crew Members
Yes, sometimes it is internal. An employee might take a drill home thinking “no one will notice.” Or they might pocket smaller items like batteries or PPE. Most of the time, it starts with a grey area—borrowing gear without permission, then never bringing it back. Without tracking, it’s hard to prove, and it becomes a habit.
2. Subcontractors and Temporary Labor
Short-term workers often get access to tools and storage without the same level of trust or accountability as your core team. If they know there’s no tracking or check-in/check-out process, they may take advantage. And once the job is done, they’re gone—along with your gear.
3. Other Trades on the Same Site
On busy sites with multiple companies working side-by-side, tools often get “borrowed” by someone from another crew who assumes it’s fine. Maybe they think it belongs to the general contractor. Maybe they’re just helping themselves. If you’re not marking and tracking your equipment, it’s easy for your assets to disappear into someone else’s trailer.
4. Outsiders and Walk-Ons
Construction sites are often wide open, especially early in the morning or late in the day. If your tools are left out or storage isn’t locked up, it takes almost nothing for someone to walk in and grab a few things. No alarm. No one notices. These thefts are quick and low-risk—especially if you’re not monitoring who comes and goes.
5. Delivery Drivers and Vendors
It sounds unlikely, but it happens. Drivers who are regularly on your site may see unattended tools or supplies and help themselves. If your deliveries aren’t supervised and you’re not tracking tools daily, this kind of theft can go unnoticed for weeks.
Theft isn’t always about bad employees—it’s about weak systems. When there’s no accountability, no tracking, and no clear ownership of gear, anyone with access can become the problem. That’s why visibility is everything. You don’t need to watch everyone—you need a system that does it for you.
How to Prevent Theft With Clear Systems and Accountability
Most theft doesn’t happen because someone’s a criminal—it happens because no one’s keeping track. When workers know tools are being monitored, stored properly, and assigned to specific people, employee theft drops fast. You don’t need to create a culture of distrust—you just need to make it clear that everything is accounted for.
Here’s how to build simple systems that reduce theft and increase accountability across your sites:
Assign Tools to People, Not Just Projects
When tools are assigned to individuals—not just jobsites—it creates responsibility. If someone knows a tool is logged under their name, they’re far more likely to take care of it and return it. Even basic sign-out processes can make a huge difference.
Use a Simple Tool Tracking System
You don’t need to micromanage, but you do need visibility. A digital tool tracking system like Remato can show you exactly who had what, when it was used, and where it was last seen. No more guessing games or chasing people down when something goes missing.
Run Weekly Spot Checks
Full audits take time, but spot checks don’t. Pick a few random items each week and make sure they’re where they should be. These quick checks not only keep people honest—they remind the team that tools are being monitored and managed.
Store Tools Like They Matter—Because They Do
Tools left in the open are tools waiting to be stolen. Lock them up after hours. Use jobsite storage boxes with real security—not just a tarp or a trailer. And make sure foremen or site leads are responsible for locking up, not “whoever’s last.”
Train Your Crew on Why It Matters
Employee theft doesn’t just hurt the company—it slows down jobs, creates tension, and adds pressure on everyone. When your crew understands that lost gear means delays, rework, and tighter budgets, they’re more likely to respect the system. Make tool accountability part of the culture, not just the paperwork.
Use Data to Spot Trends Early
If you’re tracking usage, you can see when specific tools are always going missing from the same site or crew. That helps you act before it becomes a pattern. Without data, you’re just guessing—and guessing costs money.
Preventing employee theft isn’t about distrust—it’s about building habits, using the right systems, and making it easy to stay organized. It sends a message: we value our equipment, and we expect everyone else to do the same.
How Remato Helps You Track and Protect All Your Equipment
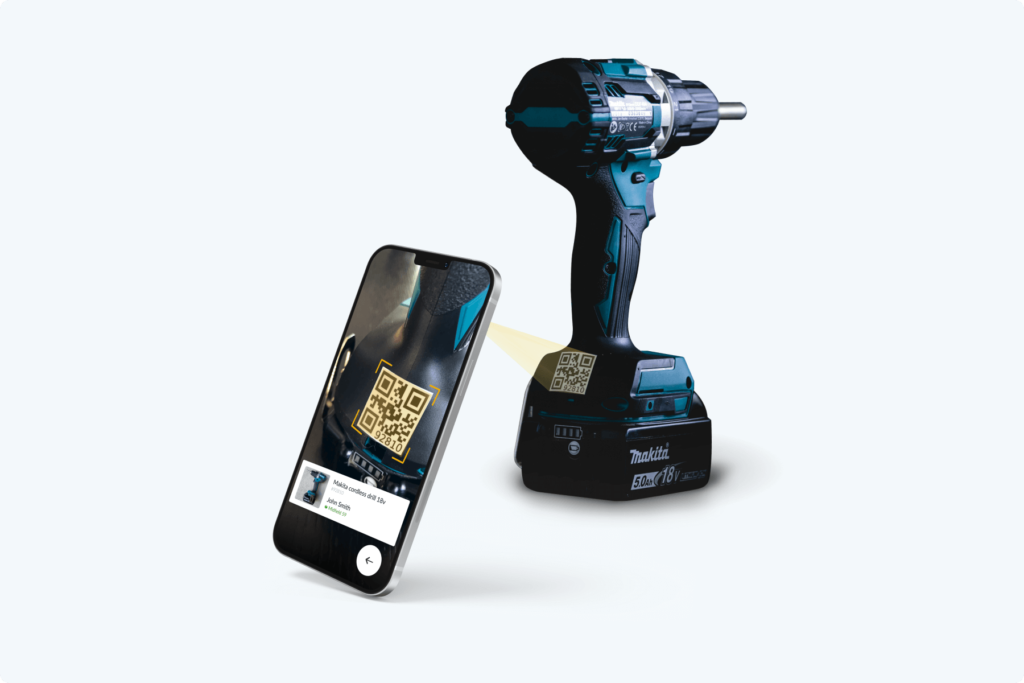
Even the best processes fall apart without the right tools. That’s where Remato comes in.
Remato’s Equipment & Tools Management system helps construction companies take control of their assets—without extra admin work or micromanagement. It gives you real-time visibility, accountability, and peace of mind. Here’s how it helps:
Tool and Equipment Assignments
Assign tools to specific workers, so there’s always a clear line of responsibility. No more “I don’t know who had it last.”
Real-Time Tracking
See who has what and where it is. Whether it’s a high-value power tool or a box of PPE, nothing falls through the cracks.
Check-In / Check-Out System with QR codes
With a simple mobile app, workers can check gear in and out from the field. No spreadsheets, no clipboards—just fast, accurate records.
Overdue Alerts and Usage Logs
Automatic alerts, plus full history of usage so you can spot patterns and potential abuse before it becomes a problem.
Field-Friendly and Office-Ready
Whether you’re on-site or in the office, Remato keeps everyone on the same page. Foremen, managers, and owners all have access to the same, up-to-date info.
By using Remato, you’re not just tracking gear—you’re building a culture of responsibility and protecting your bottom line.
Ready to stop losing tools and your profits? Try Remato for free